DMG DMU 75 monoBLOCK
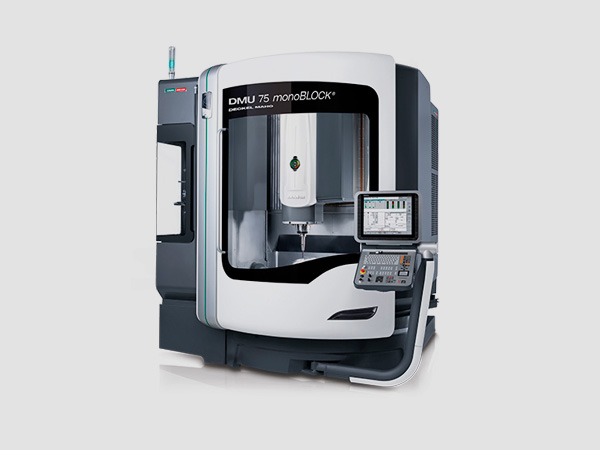
The five-axis vertical CNC machine performs the mechanical processing of mid-gauge prismatic-hull details.
The large number of tools and the five steering axes allow diverse processing on one detail. The rapid tool change and the high speed of both positioning and cutting reduce the overall production time and cost of production.
The SIEMENS 840D machine management system and the precise positioning of the mechanical part enable the production of high precision details.
Ergonomic
• Large door opening of 1310 and unique access to the working area, most compact machine with a footprint of just 8 m²
• Unrestricted crane loading of up to 600 kg
• Quick and easy to set up thanks to it´s three-point support
Precise
• Comprehensive cooling measures, high-performance coolant unit and multi-sensor compensation as standard
• Stiff construction with high static masses and balanced moving parts
Stiff monoBLOCK concept
• monoBLOCK – Maximum stability from one casting
• One-piece column with large, stable slideways, 45 mm roller guideways in all axes
• Maximum stability thanks to large ball screws in all axes ø 40 / 50 / 40
• FEM optimization of all components
Max. machinable diameter | 750 - 650 mm |
Max. X travels | 750 mm |
Max. Y travels | 650 mm |
Max. Z travels | 560 mm |
Max. table load | 600 kg |
Table diameter | 650 mm |
Maximum workable diameter | F840 mm |
Maximum workpiece height | 500 mm |
Number of tools | 60 |
Tools changeover time | 5 s |
Maximum spindle revolutions | 18,000 rpm |
Maximum speed of fast moves | 40 m/min |
Inclination of the axis A | +/- 120º |
Angle of rotation of axis C | 360º |
Distance from Spindle to table | 120 mm |
FIBER LASER ECKERT 6x2 m 4 kW
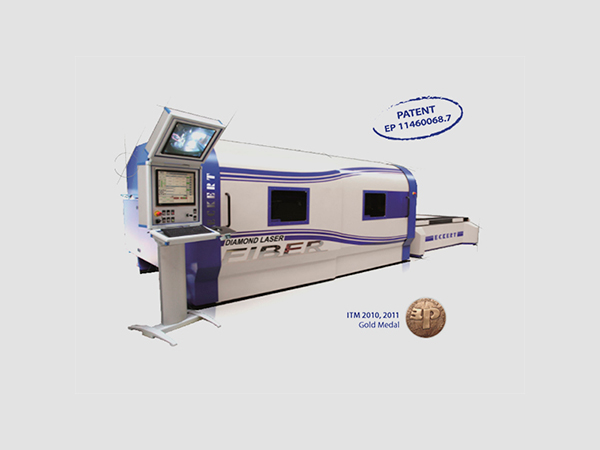
Diamond Fiber Laser cutting machine that operates with a fiber laser technology it is appropriate for laser cutting of metal sheets as well as profiles of black, stainless steel and aluminum. It is possible to cut both materials with protective foil and engraving with subsequent cutting.
These machine ensures fast speed and highest cutting precision also in complicated contours.
The high power of the machine and the accurate movements of the mechanical part guarantee precise cuts.
The large work table allows the processing of large-dimensional details.
• state-of the art cutting technology
• capability of processing a wide range of reflective materials (copper, brass, polished materials)
Future in laser cutting. High dynamics and the best cutting precision.
Model | Diamond Fiber Laser 2 |
Drives | Servo AC |
Working area | 2000 x 6000 mm |
Z axis movement | 115 mm |
Max. axis positioning speed (X,Y) | 120 m/min |
Positioning accuracy | +/- 0,03 mm |
Laser beam power | 1000 - 6000 W |
Maximum thickness for steel cutting | 18 mm |
Maximum thickness for stainless steel | 12 mm |
Maximum thickness for aluminum | 12 mm |
Laser power | 4 kW |
DMG CTX 510 ecoline
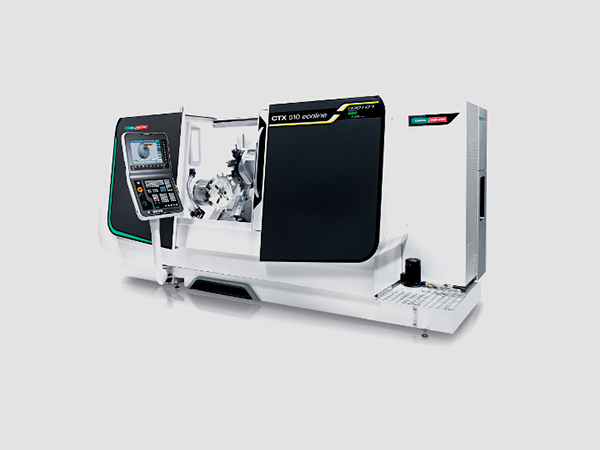
New technology with a quick change turret and 30 m/min rapid traverse. A modern CNC turning machine must be productive, flexible and easy to operate. The modern CTX ecoline model leaves nothing to be desired. This CNC turning machine is appropriate for processing of medium-dimensional details. The ability of the machine to perform both turning and milling operations in one setting of the material is of utmost importance. This contributes to improving the quality of the performed treatments and their repetition in serial work.
These complex treatments and high speeds of both positioning and cutting reduce overall production time.
The SIEMENS 840D machine management system and the precise positioning of the mechanical part enable the production of high precision details.
Highlights
• Highly dynamic spindle drive
• VDI 30 / 40 turret with up to 12 driven tool stations
• Automatic movable tailstock for maximum machining flexibility
• Digital drives and linear guides for maximum dynamics and precision
• 3D control technology: 15" SLIMline® with Operate 4.5 on SIEMENS 840D solutionline, 15" SLIMline® with HEIDENHAIN CNC PILOT 640 or 10.4" TFT screen with MAPPS IV with MITSUBISHI + DMG SMARTkey® + DMG Netservice
Swing diameter, max. | 680 mm |
Swing diameter over cross slides | 465 mm |
Turning diameter, max. | ø 465 mm |
Cross travel (X) | 300 mm |
Stroke in Z axis | 1,050 mm |
Rapid traverse (X / Z) | 30 / 30 m/min |
Number of tool stations | 12 |
Main spindle speed range, max. | 3,250 rpm |
Bar capacity | ø 76 / ø 90* mm |
UNO 20 | 40 DMG MORI
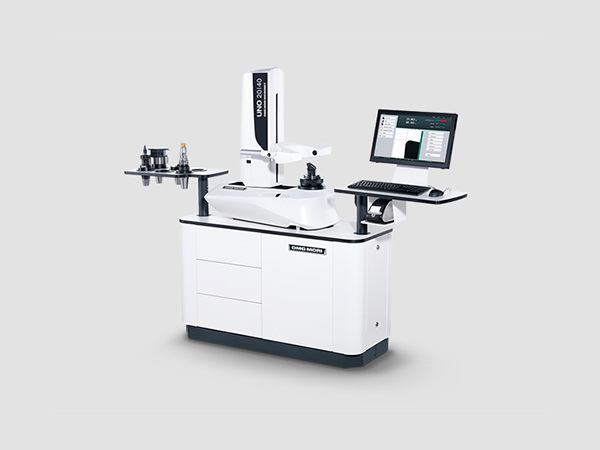
The UNO tool presetter provides accurate measurement of tools up to 400 mm in diameter and 400 mm in length. UNO 20 | 40 for manual measurement sets “new standards in the entry class of tool presetting”.
Microvision UNO quickly achieves highly accurate measuring results by using helpful functions. Accuracy is supported by a focusing window, which enables exact positioning even for highly complex tools. Another example for easy operation is MicroDock, to which up to four measuring favorites can be added via drag & drop. Furthermore, specially predefined measurement wizards simplify measuring of almost all conventional standard tools like reamers, drills or milling cutters.
Highlights
• Reamers measurable according to end gauge principle up to 100 mm diameter (traverse path up to X –50 mm)
• 19” screen with 45 times magnification
HARRIS X 6432
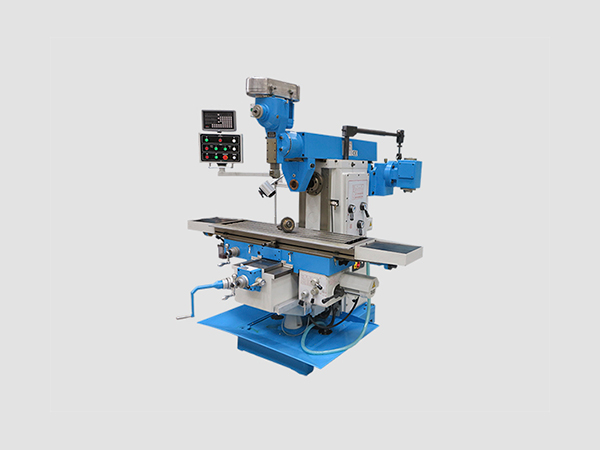
Universal milling machine for horizontal and vertical treatment of prismatic-hull details of non-ferrous metals, carbon and stainless steel trough surface milling.
Standard equipment:
Universal, rotating milling head
Automatic feed on X, Y axis
Numeric indication on 3 axes
Transition sleeve
Horizontal milling mandrels
Clamping bolt
Frontal milling cutter
Work area cooling
Work area lighting
Set of keys and tools
Model | Harris X6432 |
Machine type | SONE |
Work table size | mm 1320/320 |
X- stroke on the work table | mm 1000 |
Y- stroke on the work table | mm 300 |
Z- stroke on the work table | mm 440 |
Head offset, degrees | +/- 360 |
Drilling capacity | Ø mm 50 |
Milling capacity | Ø mm 80 |
KARMETAL KMT 350
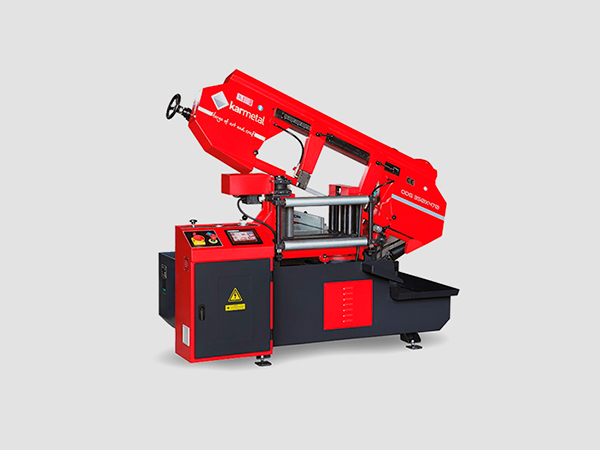
Automatic band sawing machine for cutting solid cylindrical and profile materials from ferrous and non-ferrous metals.
Manufacturer | KARMETAL-Tour. |
Model | KMT 350 ODG |
Machine type | NC |
Cutting diameter at 90 °, Ø mm | 350 |
Cutting diameter at 45 °, Ø mm | 280 |
Cutting diameter at 60 °, Ø mm | 180 |
MVD C 135 - 3100
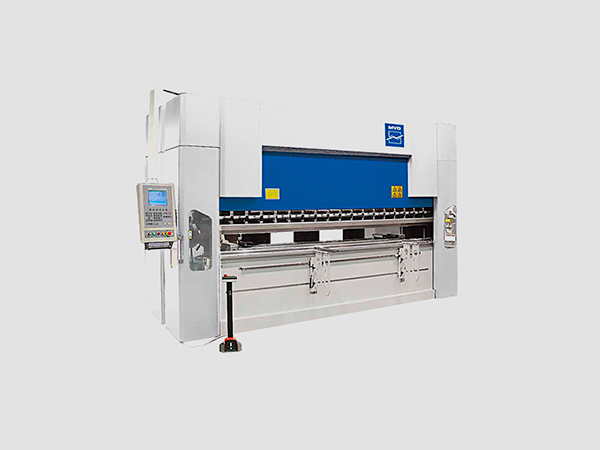
Heavy-Duty Hydraulic Swing Beam Shears serves for bending of predetermined profile of black, stainless and non-ferrous output sheeting material with a maximum folding width of 3000 mm.
Manufacturer | MVD Inan |
Model | C 135 - 3100 |
Machine type | CNC |
Working width, mm | 3100 |
Cutting capacity steel, mm | 6 |
Cutting capacity stainless material, mm | 4 |
Cutting capacity aluminum, mm | 6 |
Folding angle | 0-135° |
MVD B 06-3000
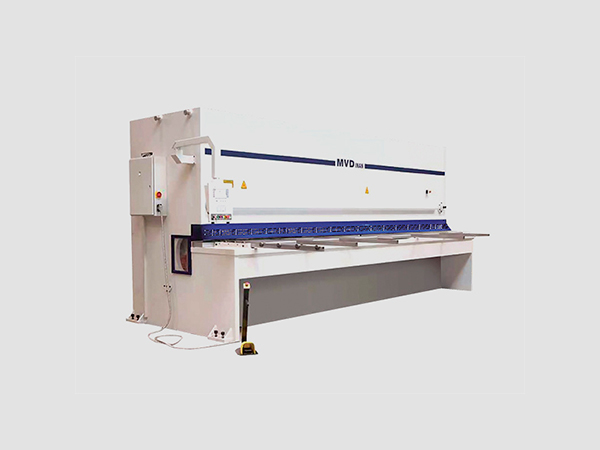
Guillotine for cutting of output sheeting material of black, stainless and non-ferrous metals with a maximum working width of 3000 mm
Manufacturer | MVD Inan |
Model | MVD B 06-3000 |
Machine type | CNC |
Working width, mm | 3100 |
Steel bending capacity, mm | 6 |
Stainless material bending capacity, mm | 4 |
Aluminum bending capacity, mm | 6 |
Folding angle | 0 - 135 ° |
POWDER COATING LINE
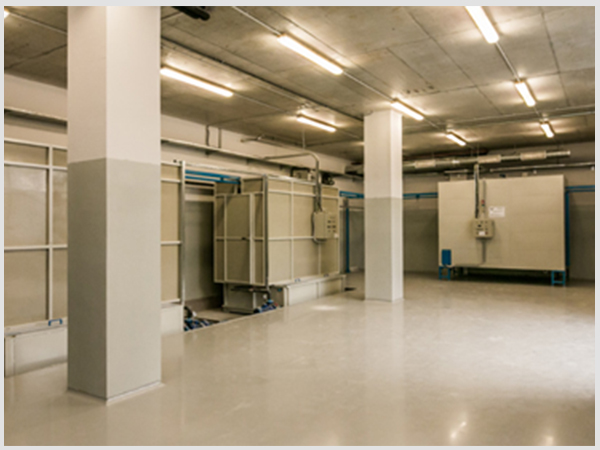
The Powder Coating Line Installation, which we have, provides high quality degreasing and powder coating line of various metals - aluminum, steel and galvanized parts. The line is very suitable for serial details coating, and its capacity enables large volumes for short periods.
Powder Coating Line is the most suitable method for coating and protecting metal products. The method has proven advantages compared to wet coating. The advantages are of a functional and aesthetic point of view. By a functional side it is guaranteed a reliable anti-corrosion protection of metal surfaces under various operating conditions, a good coating layer is guaranteed for details with a complex configuration, it enables steadiness in coverage of large details series.
The Powder Coating Line is also much more resistant to impact and scratching. By the aesthetic side, some beautiful surfaces with the desired gloss level, with relief effects, neon and luminescent effects, and many others are received as a final result. Powder coated components have less differences in appearance between horizontally or vertically coated surfaces than liquid-coated elements. The wide range of special effects is easily achievable, which is impossible to be achieved by other covering processes. Another important advantage of the Powder Coating Line is the harmless technological process and it is in conformity with the European environmental norms for production.